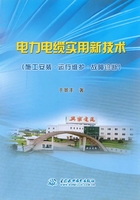
第三节 塑料绝缘电力电缆制造的工艺要求
一、拉线工艺要求
(1)铜杆或铝杆外径应均匀、圆整,结构尺寸满足公差要求;表面应清洁、无水分,
不应有皱边、裂纹、扭结、夹杂等对使用有害的缺陷。
(2)铜、铝杆的焊接:线坯采用电阻对焊。焊接压力、时间、温度及冷却时间要掌握好,焊接要牢固,接头处要用锉刀修理平整,反复弯曲两次不断。
(3)铜、铝杆的轧头:
将线坯弯成 形后,按照线坯的截面,在轧辊孔型中逐渐辗
—|
—
轧,每辗轧一次,线坯要翻转90°,轧头线坯端部呈锥形,以能穿过2~3个模孔为宜,不应有轧扁或飞边等缺陷,其长度在100~150mm。
(4)铜、铝线表面应光洁,无三角口、毛刺、裂纹、划道等机械损伤;铜线无水分、氧化变色,铝线无明显油污、腐蚀斑痕等缺陷。
(5)铜、铝单线的接头应采用电阻对焊法焊接或冷焊接,接头处直径公差不大于直径公差的2倍。硬铝线的接头应采用冷焊接,采用电阻对焊的硬铝线接头应进行退火处理,退火长度应不小于两侧各250mm。
(6)铜线润滑:采用肥皂液润滑,肥皂与水的重量比例为5∶95。(7)铝线润滑:采用38~62号汽缸油或40号汽机油润滑。
(8)收线盘应保持清洁、完好,不应有损伤单线的凸棱、翘边等不良缺陷。(9)排线应紧实、平整,不允许有相互交叉压线现象。
(10)装盘不允许过满,最外层单线与盘具侧板边缘的最小距离为15mm。
(11)铜、铝线经过拉伸后,需要采用韧炼工艺来恢复其良好的电气与机械性能。(12)吊线时要平稳、牢固,不得损伤铜单线或线盘。
(13)软化后的铜单线应软硬均匀,无过烧、过硬现象,表面不应严重氧化变色。(14)拉制的金属丝下机后应挂工序卡片,经质检员检查合格后,允许流转。
二、绞合工艺要求
(1)绞合紧压圆形线芯外径公差:25~120mm2电缆为±0.1mm,150~300mm2电
缆为±0.15mm。节距公差:按工艺附表设计规定±10mm。
(2)对于300mm2及以上大截面导体,可由半成品线芯做为中心层,然后层绞。(3)线盘张力应调节均匀,防止出现一松一紧现象。
(4)导体表面应光洁、无油污、无划伤、线芯紧压平整、无损伤屏蔽及绝缘的毛刺、锐边以及凸起或断裂的单线。
(5)裸单线接头均采用电阻对焊或冷焊接法。在同一层内,相邻两个接头之间的距离
应不小于300mm。
(6)绞合紧压导体不允许整根焊接。分头处应有明显标志,并注明准确长度。(7)排线应平整、规矩,不准有相互杂乱、交叉压线现象。
(8)计米器应计数准确。
(9)绞合紧压导体下机后应挂工序卡片,经质检员检查合格后,允许流转。
三、挤塑(绝缘)工艺要求
(1)绝缘层应连续紧密地包覆在导电线芯或缆芯上。
(2)绝缘层表面应光滑、平整,无疙瘩或塌坑,不应有连续的竹节、波浪或烧焦等。
(3)挤出的绝缘层经水槽冷却后,应通过在线火花试验装置检验无击穿点。
(4)绝缘厚度平均值,对于1.8/3kV及以下电压等级电缆,不应小于规定的标称值。(5)绝缘最薄点的测量值不应低于规定标称值的90%-0.1mm。
(6)绝缘线芯的不圆度(同一截面上的最大厚度与最小厚度的差除以最大厚度),对于3.6/6kV及以上电压等级电缆,不应超过0.15。
(7)绝缘层横断面上应没有肉眼可见的气孔、气泡、夹杂和砂眼。(8)绝缘线芯两端导体不得进水。
(9)绝缘线芯标识应首尾一致。(10)计米器应计数准确。
(11)排线应整齐、规矩,不应有相互杂乱、交叉压线现象。
(12)挤塑产品下线后应挂工序卡片,经质检员检查合格后,允许流转。
四、交联工艺要求
(1)内半导电层应均匀地包覆在导体上,表面应光滑、无明显绞线凸纹,不应有尖角、颗粒、烧焦或擦伤的痕迹,并应与绝缘层紧密结合。
(2)XLPE绝缘厚度平均值,对于1.8/3kV及以下电压等级电缆,不应小于规定的标称值。
(3)XLPE绝缘最薄点的厚度应不小于规定标称值的90%-0.1 mm。
(4)绝缘线芯的不圆度(同一截面上的最大厚度与最小厚度的差除以最大厚度),对于3.6/6kV及以上电压等级电缆,不应超过0.15。
(5)外半导电层应均匀地包覆在绝缘层上,表面应连续、光滑,不应有尖角、颗粒、竹节、波浪、烧焦或擦伤的痕迹,并应与绝缘层紧密结合。
(6)内、外半导电料及XLPE绝缘料应无杂质及混淆其他塑料颗粒,应保持干燥,不应潮湿。
(7)计米器应计数准确。
(8)排线应整齐、规矩,不应有相互杂乱、交叉压线现象。
(9)交联绝缘线芯下机后应挂工序卡片,经质检员检查合格后,允许流转。
五、金属屏蔽工艺要求
(1)铜丝屏蔽的标称截面积应根据故障电流容量确定。
(2)铜丝屏蔽由疏绕的软铜线组成,其表面应用反向绕包的铜丝或铜带扎紧,相邻铜丝的平均间隙应不大于4mm。
(3)铜带屏蔽由一层重叠绕包的软铜带组成,也可采用双层软铜带间隙绕包。铜带间的平均搭盖率应不小于15%(标称值),其最小搭盖率应不小于5%。
(4)铜带的标称厚度为:单芯电缆不小于0.12mm,三芯电缆不小于0.10mm。(5)铜带的最小厚度应不小于标称值的90%。
(6)要求绕包后平整、紧实、不折皱、不漏包,不得有卷边及碰、擦伤等不良缺陷。(7)分相标志:应用红、黄、绿色非吸湿性PP撕裂膜带、线或丝纵向放置于铜带层
内做为标志。若采用数字标志,可不放标志线。
(8)铜带断裂处应如数补足。
(9)铜带接续必须焊接,其接头处重叠均为6~10mm,焊接应牢固,并将表面处理光滑、干净。
(10)配模:按工艺规定或根据实际外径尺寸选模,确保不损伤绝缘屏蔽层。(11)计米器应计数准确。
(12)排线应整齐、规矩,不应有相互杂乱、交叉压落等现象。
(13)金属屏蔽线芯下线后应挂工序卡片,经质检员检查合格后,允许流转。
六、成缆工艺要求
(1)绕包型包带有:PVC带、聚酯带、无纺布带、阻燃带、耐火带等。(2)绝缘线芯排列规定:面对绞笼顺时针排列,红、黄、绿(PP膜色带)。
(3)配模:按工艺规定或根据缆芯实际尺寸选模,确保不损伤金属屏蔽及包带层。(4)线盘张力应调节均匀,不要出现一松一紧现象。
(5)无铠装电缆PVC绕包带应为重叠绕包,其重叠量为带宽的10%~15%,但不应小于5mm;铠装电缆聚酯带为间隙绕包,间隙量不大于带宽的40%,外层包带应全部覆盖里层包带的间隙,不允许缆芯裸露在外层包带的外面。
(6)要求包带平整、紧实、无折皱、划伤、漏包等现象。(7)包带断裂处应如数补足,接头处应用绝缘胶带粘住。
(8)填充材料应清洁、无杂质、水分和潮气等。填充不少根数,应饱满,不跳蹦,外径圆整,无明显蛇形。
(9)计米器应计数准确。
(10)排线应平整、规矩,不应有相互杂乱、交叉压落现象。
(11)成缆后的半成品应挂工序卡片,经质检员检查合格后,允许流转。
七、隔离套工艺要求
(1)隔离套应紧密包覆在缆芯上,隔离套与缆芯容易剥离,不应粘合。
(2)挤出在金属套外的隔离套经水槽冷却后,应通过在线火花试验装置检验无击穿点。(3)隔离套的标称厚度TS(单位:mm)应按下式计算
TS=0.02DU+0.6
式中 DU———挤包隔离套之前的假设直径,mm。
(4)非铅套电缆的隔离套标称厚度应不小于1.2mm,若隔离套直接挤包在铅套上,隔离套的标称厚度应不小于1.0mm。
(5)电缆冷却成形好,端头不允许进水。
(6)隔离套表面应平整、外径均匀。不得有压扁、碰抹、鼓包、松套等不良缺陷。(7)排线应平整、规矩,不应有相互杂乱、交叉压线现象。
(8)计米器应计数准确。
(9)隔离套产品下线后应挂工序卡片,经质检员检查合格后,允许流转。
八、铠装工艺要求
(1)电缆的铠装应采用适宜的金属带或金属丝铠装材料。(2)单芯电缆应选用非磁性金属带或金属丝材料铠装。
(3)配模:按工艺规定或根据缆芯实际尺寸选模,确保不损伤内层结构。(4)金属带铠装
1)金属带铠装应螺旋间隙绕包2层,使外层金属带的中线大致在内层金属带的间隙上方,包带间隙应不大于带宽的50%,外层金属带应全部覆盖里层金属带的间隙。
2)金属带接头处应剪成45°的斜口,斜口经绕包应与电缆轴线平行,接头处重叠3~
10mm并焊接牢固。
3)接头应平整、牢固,接头边缘不得有毛刺、尖角翘起等现象,并做适当防蚀处理。4)金属带铠装绕包应平整、紧实、外径均匀。
5)金属带复绕应紧密,并剔除有夹杂、毛刺、砂眼、锈蚀等缺陷的金属带。
6)金属带绕包张力的控制原则是:满盘时张力最大,否则金属带易飞出;半盘时应调松,否则会拉坏电缆或造成金属带卷边以致压伤电缆。
(5)金属丝铠装
1)圆金属丝铠装的绞合节距比为10~12,扁金属丝铠装的绞合节距比为8~10。2)金属丝绕包必须排列紧密、整齐,不得有跳浜、重叠。
3)金属丝铠装不应有大于一根金属丝直径的间隙。
4)金属丝铠装外允许疏绕一条最小标称厚度为0.3mm的金属带。
5)金属丝接头应对准中心,接头要连续、光滑、牢固,焊接处需反复弯折检查,以防虚焊。
6)复绕金属丝时,排线应平齐,不允许排成塔形或鼓形。
7)金属丝盘的张力应随时检查,各线盘的张力应均匀一致,不得有过松或过紧现象出现。
(6)金属带和金属丝铠装的绞合方向均为左向。(7)计米器应计数准确。
(8)铠装收线的排线应平整、规矩,不准有相互杂乱、交叉压落等不良现象。(9)装铠产品下线时应挂工序卡片,经质检员检查合格后,允许流转。
九、外护套工艺要求
(1)所有电缆都应具有外护套。外护套通常为黑色。
(2)挤出的外套经水槽冷却后,应通过在线火花试验装置检验无击穿点。(3)外护套的标称厚度ts(单位:mm)应按下式计算
ts=0.035D+1.0
式中 D———挤包外护套之前电缆的假设直径,mm。
(4)对于非铠装电缆和护套不直接包覆在铠装、金属屏蔽或同心导体上的电缆外护套,其厚度最小测量值应不低于标称值的85%-0.1,且单芯电缆外护套的标称厚度应不
小于1.4mm,多芯电缆外护套的标称厚度应不小于1.8mm。
(5)直接包覆在铠装、金属屏蔽或同心导体上的外护套,和1.8/3kV及以下电缆隔离套,其厚度最小测量值应不低于标称值的80%-0.2,且外护套的标称厚度应不小
于1.8mm。
(6)选配挤管式模具。
模芯孔径=护套前最大外径+(2~3)mm;
模套孔径=模芯孔径+2×模芯嘴壁厚+2×护套标称厚度+(4~5)mm。
(7)护套层应紧密包覆在缆芯上,表面应连续、光滑、圆整,无烧焦物、塑化不良、裂纹及断胶等现象,横截面上应无肉眼可见的气泡、夹杂物及砂眼等缺陷。
(8)挤出护套层冷却成形好。不得有压扁、碰伤、抹伤、鼓包、松套等缺陷。缺陷允许修补。
(9)电缆两端头不允许进水。
(10)排线应整齐、紧实、规矩,不准有交叉起落现象。
(11)采用喷码或印刷、压印标志,应字迹清晰、易于辨认,压印标志字体周围的护套厚度必须保证公差规定。
(12)计米器计数要准确,确保长度公差为≤±2‰m。(13)成品电缆交验线盘,应挂产品质量跟踪卡。
十、塑料绝缘电力电缆常见的主要质量缺陷
塑料绝缘电力电缆常见的主要质量缺陷及其原因见表158。
表158
塑料绝缘电力电缆常见主要质量缺陷及其原因

续表

续表
