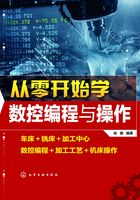
2.5 循环加工指令
切削循环是用一个含G代码的程序段完成几段走刀路线。循环指令可以简化程序,车削循环指令分为固定循环和多重复合循环。固定循环用于完成对加工表面的一次切削,多重复合循环能完成对工件某一加工面多次循环切削。
2.5.1 外圆、内径车削固定循环指令G90
外圆、内径车削固定循环指令G90包括直线切削循环和锥形切削循环。
(1) 直线切削循环G90
车削一次圆柱面,走刀轨迹:A→B→C→D→A,如图2⁃36所示,4段路线为:①AB段,刀具由循环起点快速进刀到切削起点(G00);②BC段,按给定进给速度切削外圆到切削终点(G01);③CD段,切削退刀(G01);④DA段,快速返回到循环起点(G00)。从而完成一次切削外圆。用固定循环G90指令可以完成这4段走刀路线。
直线切削循环程序段格式:G90 X(U)_ Z(W)_ F_;
程序段中,X,Z为绝对坐标编程时表示切削终点C的坐标值;U,W为增量坐标编程时表示切削终点C相对循环起点的相对坐标值。
由于“X(U)”“Z(W)”和“R”的数值在固定循环期间是模态的,如果没有重新指令“X(U)”“Z(W)”或“R”,则原来指定的数据有效。当Z轴移动量没有变化时只要对X轴指定移动指令,就可以重复固定循环,如图2⁃37所示。当指令了除G04以外的非模态G代码或指令了01组中除G90、G92、G94以外的其他G代码时这些数据就被清除。

图2⁃36 内(外)径切削循环G90
R—快速移动;F—以指定速度F移动

图2⁃37 内(外)径切削循环G90
图2⁃38中的车削固定循环程序如下。
N030 G90 U⁃8.0 W⁃66.0 F0.4; 直线切削循环第1次车削
N031 U⁃16.0; 第2次车削
N032 U⁃24.0; 第3次车削
N033 U⁃32.0; 第4次车削
例2⁃11:如图2⁃38所示,毛坯为ϕ30mm圆钢,用外圆切削循环指令编程,切削ϕ20mm外圆。

图2⁃38 G90指令切削外圆柱面
解:用G90指令编程,车削圆柱面。切削2次,每次切削深度2.5mm。
程序如下。
N05 G54; 设定右端面中心点为程序原点
N10 G00 X40.0 Z5.0; 快速定位到循环始点A
N20 G90 X25.0 Z⁃40.0 F.0.15; 第1次车削,循环路线A→B→C→D→A
N30 X20.0; 第2次车削,循环路线A→E→F→D→A
N40 G00 …; 其他程序段
注意:G90是属于01组的模态码,所以在N30程序段中仍有效,执行外圆切削循环加工,在N40段中01组的G00指令取消循环G90指令。

图2⁃39 锥形切削循环
(2) 锥形切削循环G90
锥形切削循环是车削一次圆锥面,走刀轨迹如图2⁃39所示,A→B→C→D→A。
程序段格式:G90 X(U)_ Z(W)_ R_ F_;
程序段中,X、Z为绝对坐标编程时表示切削终点C的坐标值;U,W为增量坐标编程时表示切削终点C相对循环起点的相对坐标值;R为切削起点B与切削终点C的半径差。其符号为差的符号(无论是绝对值编程还是增量值编程)。
在增量编程中地址“U”“W”和“R”后的数值的符号与刀具轨迹之间的关系如图2⁃40所示。

图2⁃40 锥形切削循环G90中U 、W和R
例2⁃12:如图2⁃41所示,粗、精加工简单圆锥零件,用G90指令编程。双点画线代表坯件。

图2⁃41 G90指令切削外圆锥面
解:程序如下。
O3353
N5 G54X100.0 Z80.0; 设定工件原点在右端面,定位到程序始点
NI0 T0101; 换刀T0101
N20 G00 X100. Z40. M03 S460; 定位到程序始点(工件原点在右端面中心)
N30 G00 X40.Z5.; 定位到循环起点
N40 G90 X31. Z⁃50. I⁃2.2 F100; 粗车圆锥面
N50 G00 X100. Z40.; 回到程序始点
N60 T0202; 换刀T0202
N70 G00 X40. Z5.; 定位到循环起点
N80 G90 X30. Z⁃50.I⁃2.2 F80; 精车圆锥面
N90 G00 X100. Z80.; 回到程序始点
N100 M05; 主轴停转
N110 M30; 程序结束
例2⁃13:零件如图2⁃42所示,双点画线为工件毛坯,编写粗、精车外圆和锥面的程序。

图2⁃42 粗、精车外圆和锥面
解:程序如下。
O4132;
N10 T0101; 换刀T0101
N20 M03 S460; 启动主轴,转速460r/min
N30 G00 X100. Z40.; 定位到程序始点
N40 X40. Z3.; 定位到循环起点
N50 G80 X31. Z⁃50. F100; 粗车圆柱面,到尺寸ϕ31mm×50mm
N60 G80 X25. Z⁃20.; 粗车“ϕ24”圆柱面,到尺寸ϕ25mm×20mm
N70 G80 X29. Z⁃4. I⁃7. F100; 粗车“ϕ28”圆锥面,到尺寸ϕ29mm
N80 G00 X100. Z40.; 回到程序始点
N90 T0202; 换刀T0202
N100 G00 X100. Z40.; 定位到程序始点
N110 G00 X14. Z3.; 定位到精车始点
N120 G01 X24. Z⁃2. F80; 倒角“C2”
N130 Z⁃20.; 精车“ϕ24”圆柱面
N140 X28.; 车台阶面
N150 X30. Z⁃50.; 精车“ϕ28”圆锥面
N160 G00 X36.; 快速退刀
N170 X100. Z40.; 回到程序始点
N180 M30; 程序结束
2.5.2 端面车削循环指令G94
端面车削循环G94包括平端面切削循环和锥面切削循环。
(1)平端面切削循环G94
用G94指令切削一次端平面,走刀轨迹如图2⁃43所示,即A→B→C→D→A。4段路线为:①AB段,刀具由循环起点始快速进刀到切削起点;②BC段,按给定进给速度切削端面到切削终点;③CD段,工进退刀;④DA段,快速返回到循环起点。从而完成一次切削端面。用G94指令完成这4段走刀路线。
程序段格式:G94 X(U)_ Z(W)_ F_;
程序段中,X,Z为绝对坐标编程时表示切削终点C的坐标值;U,W为增量坐标编程时表示切削终点C相对循环起点的相对坐标值。
(2)锥面切削循环G94
用G94指令切削一次圆锥端面,走刀轨迹如图2⁃44所示,即A→B→C→D→A。

图2⁃43 平端面切削循环G94
X,Z—绝对坐标值;U,W—相对坐标值;R—快速移动;F—以指定速度F移动

图2⁃44 圆锥端面切削循环G94
程序段格式:G94 X(U)_ Z(W)_ R_ F_;
程序段中,X,Z为绝对坐标编程时表示切削终点C的坐标值;U,W为增量坐标编程时表示切削终点C相对循环起点的相对坐标值,符号如图2⁃45所示;R为切削起点B相对于切削终点C的Z轴方向的有向距离,符号如图2⁃45所示。

图2⁃45 锥面切削循环G94中U 、W和R
例2⁃14:零件如图2⁃46(a)所示,双点画线为工件毛坯,编写切削工件圆锥端面程序。

图2⁃46 锥面切削循环编程例题
解:程序如下。
O3543;
N10 T0101; 选一号刀
N20 G00 X60.0 Z45.0; 快速定位到循环起点
N30 M03 S460; 主轴正转
N40 G94 X25.0 Z33.5 R⁃3.5 F100; 切削起点距工件外圆2.5mm,故“R”值为-3.5,如图2⁃46(b)所示
N45 Z31.5; 每次吃刀均为2mm
N50 Z29.5;
N60 Z27.5;
N70 Z25.5; 第5次循环切削,吃刀深2mm
N80 G00 M05; 取消切削循环,主轴停
N90 M30; 主程序结束
2.5.3 外圆粗车多重循环指令G71
固定循环只完成对加工表面的一次切削,多重循环指令能进行多次循环切削,在多重循环指令的程序中只需写出工件精加工的形状数据,系统自动生成多次粗加工切削轨迹。
(1)粗车多重循环G71
粗车多重循环指令G71完成的切削图形如图2⁃47所示,刀具路线是从A到A',再到B的精加工形状,在指定的区域每次进刀切去Δd(切深),精车余量为 Δu/2 和Δw。

图2⁃47 外圆粗加工多重循环G71
(F)—切削进给;(R)—快速移动
程序格式:G71 U(Δd) R(e);
G71 P(ns) Q(nf) U(Δu) W(Δw) F(f) S(s) T(t);
其中 Δd——每次切削深度(半径值),无正负号;
e——每次循环后的退刀量(半径值),无正负号;
ns——精加工程序第一个程序段的段顺序号;
nf——精加工程序最后一个程序段的段顺序号,从ns到nf程序段为精车路线,即工件精加工的形状数据;
Δu——X方向的精加工余量,直径值;
Δw——Z方向的精加工余量;
f,s,t——粗加工时G71中编程的F、S、T有效,精加工时处于ns到nf程序段之间的f、s、t有效,如果没设定,则精加工时按照G71中编程F、S、T执行。
(2)G71多重循环功能
① G71多重循环粗车切削沿平行Z轴方向进行,如图2⁃47所示,图中A点为循环起点,A'点为精车始点,B点为精车终点,段顺序号ns至nf之间的程序段是精车路线,即工件精加工的形状数据。
② G71多重循环切除棒料毛坯大部分加工余量,经过G71多重循环切削后,工件尚留有精车余量,即Δu、Δw。
(3)编程要点
G71多重循环编程,如图2⁃47所示,要确定图中的循环切削换刀点、循环始点C、精车始点A'和切削终点B的位置坐标。循环始点C的X、Z坐标均应位于毛坯尺寸之外。为节省数控机床的辅助工作时间,从换刀点至循环始点C使用G00快速定位指令,
G71指令程序段中有两个代码“U”,前一个表示背吃刀量,后一个表示X方向的精车余量。在程序段中有“P”“Q”代码,则代码“U”表示X方向的精加工余量,反之表示背吃刀量。背吃刀量无负值。
2.5.4 精车循环指令G70
工件经G71、G72或G73指令粗车后,尚留有精加工余量Δu、Δw,如图2⁃47所示,用G70精车循环,可切除精车余量Δu、Δw,实现精加工。精车循环G70程序格式:
程序格式:G70 P(ns) Q(nf);
程序段中 ns——精加工程序第一个程序段的顺序号;
nf——精加工程序最后一个程序段的顺序号。
执行精车G70时在G71、G72、G73 程序段中规定的F、S 和T功能无效,ns和nf之间指定的F、S和T有效。当G70循环加工结束时刀具返回到起点并读下一个程序段。G70 G71、G72、G73 中ns到nf间的程序段不能调用子程序
例2⁃15:零件如图2⁃48所示,毛坯为ϕ40mm圆钢,用车削循环指令编程,粗、精车加工。

图2⁃48 外圆粗、精加工循环应用
解:用G71、G70指令粗车和精车外圆程序。
车削程序如下。
N005 G54 设定工件右端面中心点为程序原点
N010 G00 X150.0 Z100.0 S800 M03 T0202; 快速定位到程序始点K
N020 G00 X41.0 Z2.0.; 快速定位到循环始点A
N030 G71 U2.0 R 1.0; 粗车循环
N040 G71 P50 Q120 U0.5 W0.2 F0.2; 粗车循环
N050 G00 X0; 定位到精车切入点B,精车路线开始段
N055 G01 Z0; 切入到C
N060 G03 X11.0 W⁃5.5 R5.5; 切弧CD
N070 G01 W⁃10.0; 直线DE
N080 X17.0 W⁃10.0; 直线EF
N090 W⁃15.0; 直线FD
N100 G02 X29.0 W⁃7.348 R7.5; 弧GH
N110 G01 W⁃12.652; 直线HI
N120 X41.0; 切出,直线IJ,精车路线结束段
N130 G70 P50 Q120 F0.1; 精车循环
N140 G00 X150.0 Z100.0; 回到起始位置
N150 M30; 程序结束
2.5.5 平端面粗车循环指令G72
平端面粗车循环G72的循环切削路线平行于X轴,该循环程序段格式与G71完全相同。
G72 U(Δd) R(e);
G72 P(ns) Q(nf) U(Δu) W(Δw) F(f) S(s) T(t);
程序段中,Δd、e、ns、nf、Δu、Δw的含义与G71相同。
如图2⁃49所示,G72循环加工是由平行X轴的轨迹完成的,除此之外,该循环与G71 完全相同。
例2⁃16:零件如图2⁃50所示,毛坯为ϕ45mm圆钢,用端面粗车循环指令编程,粗、精车加工。

图2⁃49 平端面粗车(G72)

图2⁃50 端面粗、精加工循环应用
解:用G72与G70粗、精车端面和外圆的程序如下。
N005 G54 S700 M03 T0303; 设定工件右端面中心点为程序原点
N010 G00 X150.0 Z100.0; 快速定位到程序始点
N020 G00 X41.0 Z1.0; 定位到循环始点A
N030 G72 W3.0 R 1.0; 粗车循环
N040 G72 P050 Q070 U0.4 W0.2 F0.3; 粗车循环
N050 G00 X14.0 Z1.0; 定位到精车切入点B(精车开始)
N055 G01 X20.0 Z⁃2.0 F0.15; 切削,倒角
N060 Z⁃20.0; 车圆柱面
N065 X40.0 Z⁃30.0; 车锥面
N070 X45.0; 切出(精车结束)
N080 G70 P50 Q80; 精车循环
N090 G00 X150.0 Z100.0; 回到起始位置
N100 M30; 程序结束
2.5.6 型车复合循环指令G73
型车复合循环G73在切削工件时刀具轨迹如图2⁃51所示的封闭回路,刀具逐渐进给,使封闭切削回路逐渐向零件最终形状靠近,并最终切削成工件的形状。对铸造、锻造等粗加工中已初步成形的工件,G73指令可以进行高效率切削。程序格式:
G73 U(Δi) W(Δk) R(d);
G73 P(ns) Q(nf) U(Δu) W(Δw) F(f) S(s) T(t);

图2⁃51 型车复合循环(切削固定形状)
其中 Δi——X轴方向总退刀量(半径值);
Δk——Z轴方向总退刀量;
d——循环次数;
ns——精加工程序第一个程序段的顺序号;
nf——精加工程序最后一个程序段的顺序号;
Δu——X方向的精加工余量(直径值);
Δw——Z方向的精加工余量;
f,s,t——粗加工时G73程序段中的F、S、T地址有效,精加工时处于ns到nf程序段之间的F、S、T地址有效。
Δi和Δk是粗加工时总的切削量(粗车余量),粗加工次数为d,则每次X轴和Z轴方向的背吃刀量分别为Δi/d和Δk/d。Δi和Δk值的设定与工件的背吃刀量有关。
型车复合循环的特点是刀具轨迹平行于工件的轮廓,适合加工铸造、锻造成形或已经粗车成形的工件,由于此类零件毛坯具有工件的形状,用G73指令有利于减少空行程,提高切削效率。
采用型车复合循环G73编写程序时,需要确定换刀点、循环始点D、精车始点A'、精车终点B的坐标位置。图2⁃52中,D点为循环始点,A'→B是工件的轮廓线,A→A'→B为刀具的精加工路线,粗加工时刀具从A点后退至C点,后退距离分别为Δi+Δu/2,Δk+Δw,粗加工循环之后自动留出精加工余量Δu/2、Δw。顺序号ns至nf之间是精加工程序。

图2⁃52 型车复合循环G73应用
例2⁃17:零件如图2⁃52所示,毛坯为锻件,用型车复合循环指令编程,编制粗、精车加工的程序。
解:用G73与G70粗、精车锻造毛坯工件。程序如下。
N005 G54 S600 M03 T0304; 设定工件右端面中心点为程序原点
N010 G00 X260.0 Z 220.0; 快速定位到程序始点
N020 G00 X220.0 Z160.0; 定位到循环始点B
N030 G73 U14.0 W14.0 R3.0; 粗车循环
N040 G73 P050 Q80 U1.0 W0.5 F0.3; 粗车循环
N050 G00 X80.0 W⁃40.0; 定位到精车切入点,精车开始
N055 G01 W⁃20.0 F0.15; 车圆柱面“ϕ80”
X120.0⁃W10.0; 车锥面
N060 W⁃20.0; 车圆柱面“ϕ120”
N070 G02 X160.0 W⁃20.0 R20.0; 车圆弧“R20”
N080 G01 X180.0 W⁃10.0; 车锥面,精车结束
N090 G70 P50 Q80; 精车循环
N100 G00 X260.0 Z220.0; 回到起始位置
N110 M30; 程序结束
例2⁃18:图2⁃53所示零件毛坯为锻件,图中双点画线部分为工件毛坯。编制零件的加工程序,要求设切削起始点在A(60,5),X轴、Z轴方向粗加工余量分别为3mm、0.9mm,粗加工次数为3,X轴、Z轴方向精加工余量分别为0.6mm、0.1mm。

图2⁃53 锻件毛坯零件的编程应用
解:程序如下。
O550
N10 T0101; 设立坐标系,选一号刀
N20 G00 X80. Z80.; 定位到程序起点
N30 M03 S800; 主轴以800r/min正转
N40 G00 X60. Z5.; 定位到循环始点
N50 G73 U3. W0.9 R3. P60 Q140 X0.6 Z0.1 F120; 闭环粗切循环加工
N60 G00 X0 Z3.; 精加工轮廓开始,到倒角延长线处
N70 G01 U10. Z⁃2. F80; 精加工倒角“C2”
N80 Z⁃20.; 精加工“ϕ10”外圆
N90 G02 U10. W⁃5. R5.; 精加工“R5”圆弧
N100 G01 Z⁃35.; 精加工“ϕ20”外圆
N110 G03 U14. W⁃7. R7.; 精加工“R7”圆弧
N120 G01 Z⁃52.; 精加工“ϕ34”外圆
N130 U10.W⁃10.; 精加工锥面
N140 U10.; 退出已加工表面,精加工轮廓结束
N150 G00 X80.Z80.; 返回程序起点位置
N160 M30; 主轴停、主程序结束并复位